views
How to Machine Undercuts: A Practical Guide
Machining undercuts demands specialized strategies, tooling, and machine capabilities. Whether you’re creating a groove for a retaining ring or a hidden clearance pocket, these steps will guide you through the process:
-
Design and Drawing Preparation
-
Specify undercut dimensions (depth, width, angle, corner radius) clearly using GD&T symbols.
-
Indicate surface finish requirements.
-
Provide a note on tool access angle or machine axis orientation if critical.
-
-
Tool Selection
-
For straight undercuts: choose L-shaped or bull-nose undercut cutters with rigid shanks.
-
For angle undercuts: use dovetail or form-profile tools.
-
For internal undercuts on a lathe: live tooling with angular holders or slidetrueing tools.
-
-
Machine Capability Assessment
-
Confirm access: 3-axis vs. 3+2 vs. full 5-axis milling.
-
Ensure sufficient clearance for tool tilt and holder.
-
Verify through-tool coolant availability for chip evacuation.
-
-
CAM Programming
-
Define clearance and retract planes to avoid collision.
-
Set multi-axis tool orientation: tilt angle, axis rotation limits.
-
Break the undercut into multiple shallow passes to reduce tool deflection.
-
Simulate the full toolpath in CAM software, checking for gouges or collisions.
-
-
Cutting Parameters
-
Use conservative depths of cut and light radial engagement.
-
Increase spindle speed to compensate for small cutter diameters.
-
Maintain proper chip load to avoid rubbing and heat buildup.
-
-
Chip Control
-
Employ high-pressure coolant or air to clear the recess.
-
Program cyclic retractions to shake loose chips.
-
Polish flute surfaces on carbide cutters to reduce chip adhesion.
-
-
Fixturing and Workholding
-
Ensure stable clamping to counteract cutting forces.
-
For deep undercuts, consider angle plates or vacuum fixtures to maximize access.
-
-
Inspection and Quality Assurance
-
Use bore scopes, air gauges, or CMM probes to measure hidden features.
-
Verify undercut depth, width, and surface finish against drawing callouts.
-
Document results in an inspection report for traceability.
-
By following this structured approach, machinists can reliably produce undercuts that meet tight tolerances and surface requirements. Each step—from design clarity to final inspection—plays a pivotal role in successful undercut machining.
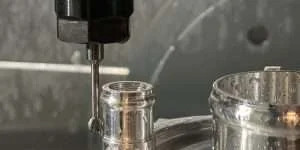
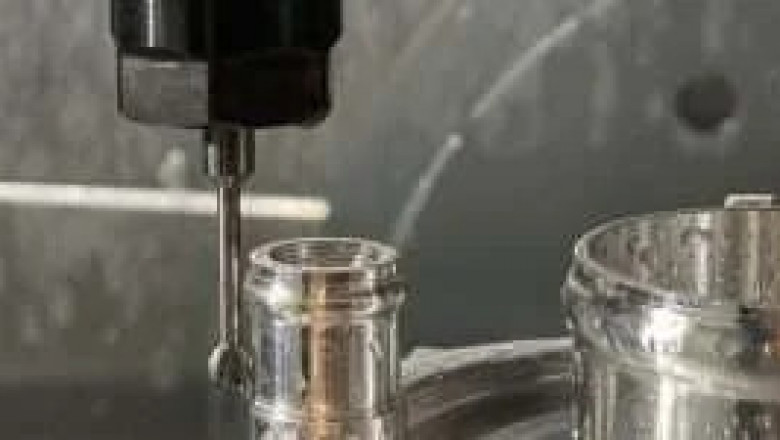

Comments
0 comment